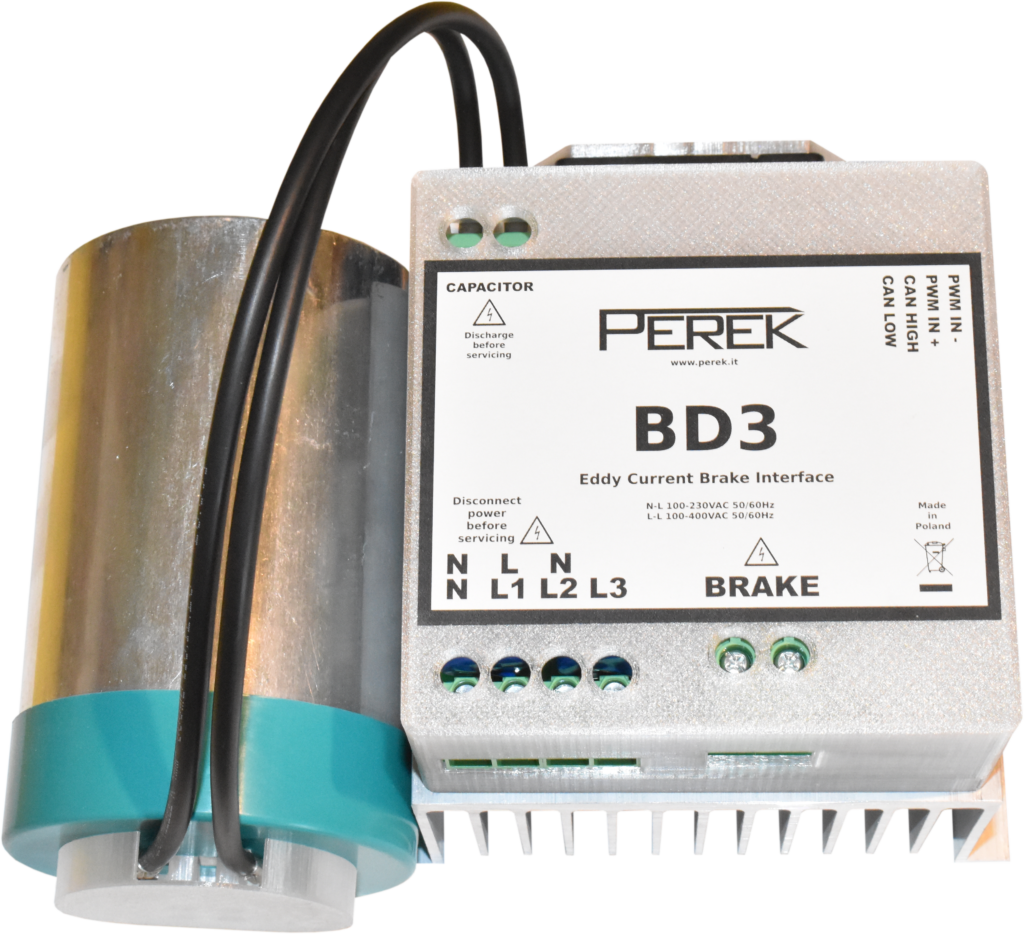
BD3 Brake Power Supply is intended to interface mains supplied eddy current brakes with dynamometer controller. It is used to keep brake current at the level required to get desired torque. BD3 offers one or three-phase mains input and fast demagnetization circuit for quicker brake response. With BD3, typical dyno brakes will deliver full torque output under 0.2s and will completely turn off under 0.02s. Fast brake response is especially beneficial in dynamometers with low inertia, such as engine dynamometer or hub dynamometer.
BD series brake power supplies comparison
Safety precautions
- The device should be fixed on a hard, flat surface in a well-ventilated area.
- The device must not be exposed to vibration.
- The device air flow must not be obstructed.
- No foreign objects should be inserted into the device.
- Life-threatening, high voltages are present in the device. Make sure that it is disconnected from mains power supply before doing maintenance work.
- The device is equipped with high voltage storage capacitor. Before servicing the device, after disconnecting power, wait until the capacitor voltage to drops to a safe level.
- The capacitor must be connected to BD3 to discharge on its own. A charged capacitor disconnected from BD3 will hold dangerous charge for many days if not discharged.
- When operating under load, the device radiator will get hot. Before servicing the device wait until it cools down.
- The device is intended for installation by qualified personnel.
- The device must be installed in a closable electrical cabinet and protected from access by unskilled personnel.
- The device should be protected from moisture. It mustn’t be used when wet.
- The device should be protected from ingress of conductive contaminants. It shouldn’t be operated where metal grinding or cutting dust is present in the air.
- The device mustn’t be powered without the enclosure assembled.
- Device installation doesn’t require enclosure disassembly.
- If the device is not working correctly, makes disturbing noises, emits burning smell, it should be immediately powered down. Please contact the manufacturer for repair.
- All dyno metal elements must be connected to safety ground. Any short circuit of live wire to dyno chassis must result in circuit breaker opening. Use of RCD breaker is advised for additional safety.
- Device power supply must be protected with over current circuit breaker with D characteristic. The breaker value should be selected to a minimum that is sufficient to supply the brake.
- The mains power connection must contain a switch that will provide a way to disconnect the device from the grid.
device variant | one phase supply | three phase supply |
---|---|---|
BD3 – 22.5A | 25A | 16A |
BD3 – 30A | 32A | 25A |
BD3 – 45A | 32A |
Specification
Supply | 1 or 3 phase L-N 100-240VAC L-L 100-415VAC 50/60Hz |
Electrical connections | Supply and capacitor: up to 4mm² (10 AWG) Brake output: up to 16mm² (6 AWG) |
Continuous current rating | BD3-22.5A: 22.5A @ 40°C ambient temperature BD3-30A: 30A @ 40°C ambient temperature BD3-45A: 45A @ 25°C ambient temperature 40A @ 40°C ambient temperature |
Brake discharge method | Fast discharge with storage capacitor |
Switching frequency | Adaptive, up to 4kHz |
Brake current control | Controlled with microcontroller in closed loop |
Dimensions | 22.5A, 30A: 14cm x 15.5cm x 12cm 45A: 26cm x 23.5cm x 11cm |
Current target control | Programmable current range Galvanically isolated PWM input, 15Hz – 4kHz, 4V – 8V, higher input voltage allowed with external resistor Galvanically isolated CAN bus interface, CAN-BUS 2.0B, 500kBit |
Diagnostics | CAN bus: Brake current Power stage temperature Switching frequency Additional information possible in future with firmware updates |
Operating ambient temperature | −20°C ÷ 50°C |
Operating humidity | 0% ÷ 95% without condensation |
Elevation | Up to 2000 m.a.s.l. |
Mass | 22.5A, 30A: 1.3kg 45A: 3.3kg |
Grid current use
The current that is required from grid depends on many factors, such as the absorber DC current, absorber resistance and grid supply voltage. Here are some typical cases:
1 phase 230VAC supply, 192V absorber
The required current will be equal or a bit more than the absorber current. If the absorber current is above typical 16A circuit breaker, that may cause it to trip if the load is high for long period. For example if the eddy brake current is 22A, then a 16A circuit breaker may trip after 200 seconds.
3 phase 400VAC supply, 192V absorber
Due to use of 3 phases and higher voltage available at the supply side, the current per phase will be lower than the absorber DC current. Usually peak current per phase will be around 1/3 to 1/2 of the absorber current. This allows for care free use of absorbers that require more than 16A of current.
1 phase 230VAC supply, 96V absorber
The average grid current will be lower than the absorber current, because due to voltage difference, BD3 will be switching the power to the absorber only part of the time. In the end the same absorber wired for 96V will use a bit more current than the one wired for 192V, but the 96V will require more powerful BD3 version.
BD3 similarly to other devices that rectify current like for example VFDs, draw current not only at the base mains frequency, but also at harmonic frequencies. This creates apparent power use higher than the active power. Reduction of harmonic current and apparent power can be achieved with use line reactor at the BD3 power supply input. The reactor should be placed before line filter.
Device connection
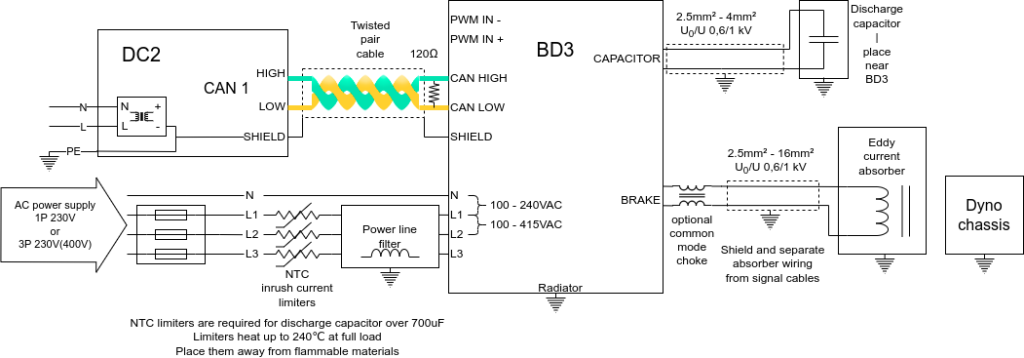
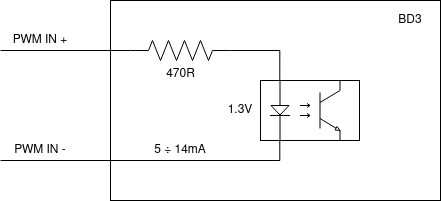
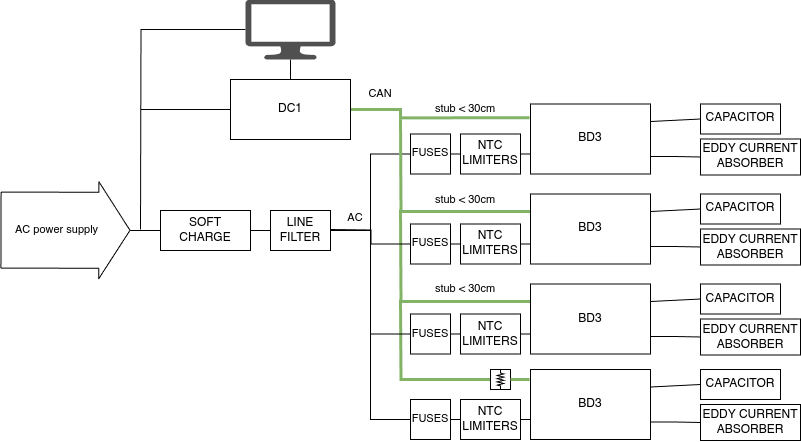
If you have a dyno with multiple BD3 and you plan to switch them all at once, then Soft Charge Kit is useful to avoid tripping main fuse, when all BD3 capacitors are charged at once.
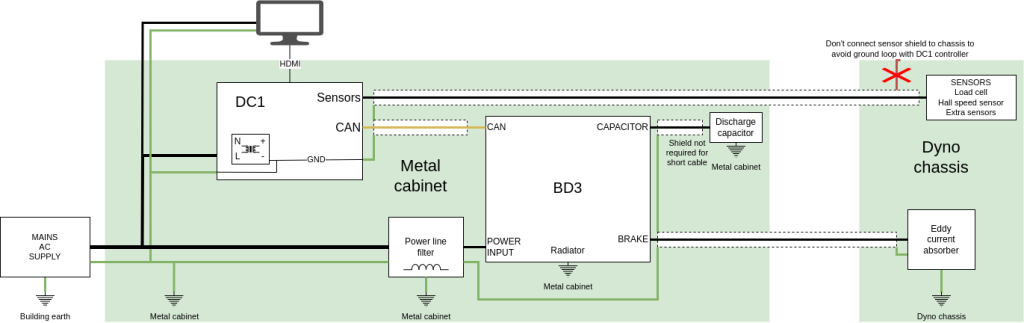
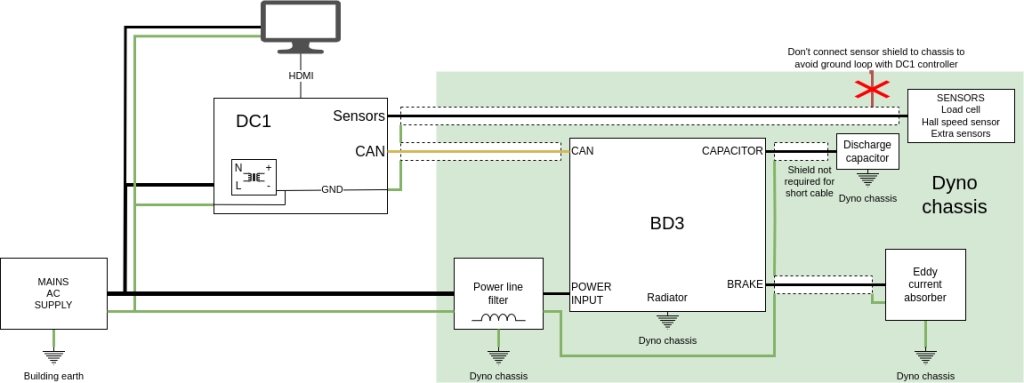
Terminal | Description |
---|---|
PWM IN- | PWM input negative |
PWM IN+ | PWM input positive |
CAN HIGH | CAN bus high |
CAN LOW | CAN bus low |
N / N | Mains supply neutral |
L1 / L | Mains supply phase |
L2 / N | Neutral for 1 phase connection 2nd phase for 3 phase connection |
L3 | Mains supply phase |
CAPACITOR | Discharge capacitor connector |
BRAKE | Eddy current brake connector |
Terminal | 1 phase connection | 1 phase alternative | 3 phase connection | 3 phase connection low L-L |
---|---|---|---|---|
N / N – REQUIRED | N – Neutral | L – Phase | N – Neutral | L2 – Phase 2 |
L1 / L – REQUIRED | L – Phase | N – Neutral | L1 – Phase 1 | L1 – Phase 1 |
L2 / N – REQUIRED | N – Neutral | L – Phase | L2 – Phase 2 | L2 – Phase 2 |
L3 – OPTIONAL | L3 – Phase 3 | L3 – Phase 3 | ||
Notes: | N-L: 100 – 240VAC All three terminals must be connected | N-L: 100 – 240VAC All three terminals must be connected | N-L1: 100 – 240VAC L-L: 100 – 415VAC | L-L: 100 – 240VAC |
Note: In case of some 1 phase AC mains plugs, the plug can be reversed in the socket and swap N with L. It’s not a problem. The main concern while connecting mains supply to the BD3 is not to make a connection that will create voltage higher than 240VAC between N/N and L1/L terminals.
The use of discharge capacitor with capacity higher than 700uF require installation of NTC inrush current limiters on the BD3 supply to avoid excessive current when charging empty capacitor. The limiters and rail terminal blocks are provided with the capacitor.
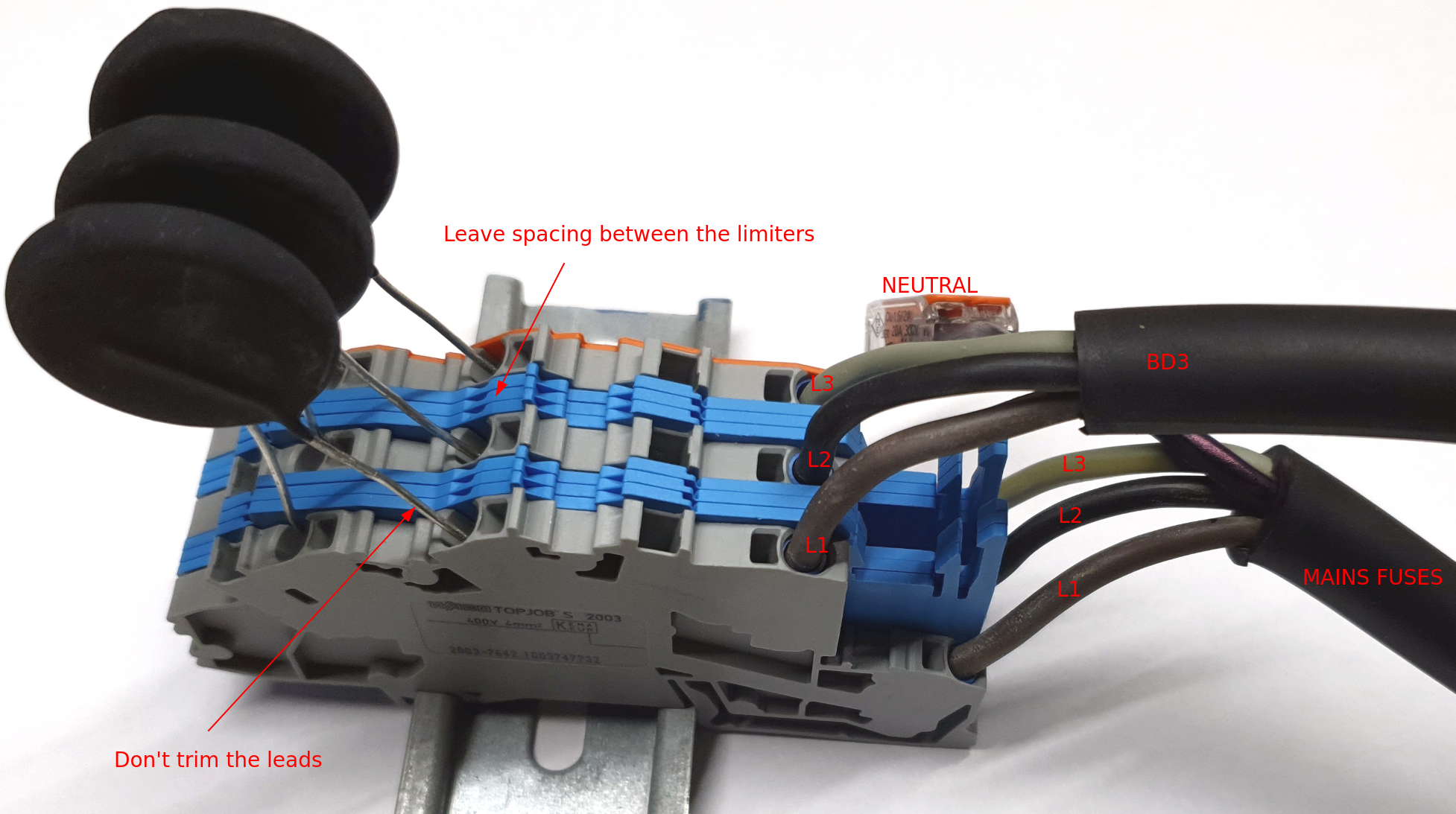
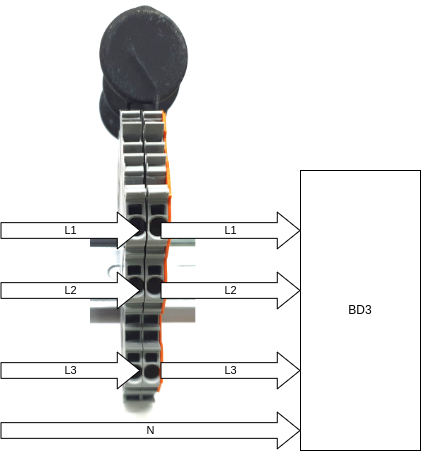
WARNING! Voltages in the device are life-threatening.
All connections should be made with the device disconnected from main supply.
Connecting the supply is allowed only when the device is safely installed, and its enclosure is assembled.
Storage capacitor keeps dangerous voltages present in circuit for 15min (250uF) or 30min (600uF) after mains disconnection.
Wait for capacitor to discharge before servicing.
PWM and CAN circuits are isolated from dangerous voltages and are the only circuits safe to touch when the device is powered on.
Capacitor and brake wiring should be routed away from sensitive circuits (i.e. load cell cable). If separate routing is not possible, shielded wiring should be used.
The typical required cross-section of power cables for operation in 40°C is:
- 2.5mm² up to 17A
- 4mm² up to 23A
- 6mm² up to 30A
- 10mm² up to 40A
- 16mm² up to 50A
Discharge capacitor
The device uses a discharge capacitor for storing brake demagnetization energy and for filtering mains input voltage. Typical voltage present on the capacitor is 325VDC for 230VAC supply or 564VDC for 400VAC supply. When the brake is quickly discharged from high current, capacitor voltage will temporarily rise up to 1000V.
For fast demagnetization to work properly, the capacitor must be sufficiently sized. The minimum required capacitance value can be calculated using the calculator below. To select the optimal capacitor for your brake, please contact us.
Eddy current brake peak current
A
Eddy current brake inductance
mH
Magnetic energy in brake
J
Minimum capacitance
uF
BD3 must be always operated with discharge capacitor connected. Operating the BD3 without the capacitor can lead to device damage not covered under warranty.
Absorber compatibility
To be suitable for use with BD3, the absorber insulation must withstand temporary voltage spikes up to 1000V. Typical absorber wire insulation is rated to withstand 2kV – 8kV from turn to turn. Good design can further increase breakdown voltage of the whole absorber. If you’re not sure if your absorber have suitable breakdown voltage, contact your manufacturer.
The following absorber brands are confirmed compatible with BD3:
Absorber brand | Factory insulation voltage test |
---|---|
Frenelsa | 1500V |
KLAM | 1500V |
Pentar Kloft | 5000V |
Elektromex Centrum | 1000V |
Borghi & Saveri | 1000V to 2500V |
When installing BD3 with an old, used absorber, check the wiring condition first with insulation tester set to minimum 1500V. Running BD3 with an absorber that has faulty insulation will lead to BD3 device damage.
To keep your absorber insulation healthy for the longest, adhere to the following guidelines:
- Don’t overheat the coils
- Don’t exceed nominal current
- Don’t power the brake which is not rotating
- Run the brake idle for some time after a heavy run to allow it to cool down
- Don’t overheat the plates
- When the plates start to glow red, stop loading the brake and run it in idle to cool down. Don’t just stop driving, as this will cause the heat to move to the coils and bearings.
- Avoid mechanical damage to the coils
- Keep the moisture and mold away
- Avoid coils contamination with dust or fluids
According to eddy brake manufacturers, the safe operating temperatures are 170°C for coils and 600°C for plates. Keep in mind that coils internal temperature during operation will be higher than the surface temperature.
Programming and operation
Best way to connect BD3 brake interface with DC series dynamometer controller is via CAN-BUS. Twisted pair cable must be used. 120Ohm terminating resistor must be placed on bus ends. On the DC end, a built-in terminator resistor can be used. For more information, refer to Wikipedia page on CAN bus.
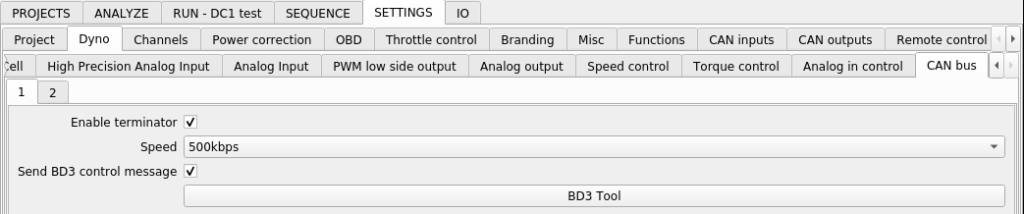
Example CAN bus setup for BD3 require:
- Speed: 500kbps
- Send BD3 control message: checked
Enable terminator can be checked if CAN bus has one end in DC controller.
CAN id | Description | Format |
---|---|---|
0x160 | Programming communication from DC to BD3 | |
0x161 | Programming communication reply from BD3 to DC | |
0x162 | Control message with desired current information [16bit current fraction 0x0 ÷ 0xffff big endianness] 0x0 = 0% of current range 0xffff = 100% of current range | [ channel 1 and 5 ] [ channel 2 and 6 ] [ channel 3 and 7 ] [ channel 4 and 8 ] |
0x163-0x16A | BD3 status message [each field 16bits, big endianness] 0x163: channel 1 0x164: channel 2 0x165: channel 3 0x166: channel 4 0x167: channel 5 0x168: channel 6 0x169: channel 7 0x16A: channel 8 | [ output current 10mA/bit (45A version) 5mA/bit (22.5A version) ] [ output switching frequency 100Hz/bit ] [ power module temperature 0.1°C/bit signed ] [ reserved ] |
BD3 interface should be configured with BD3 Tool before use.
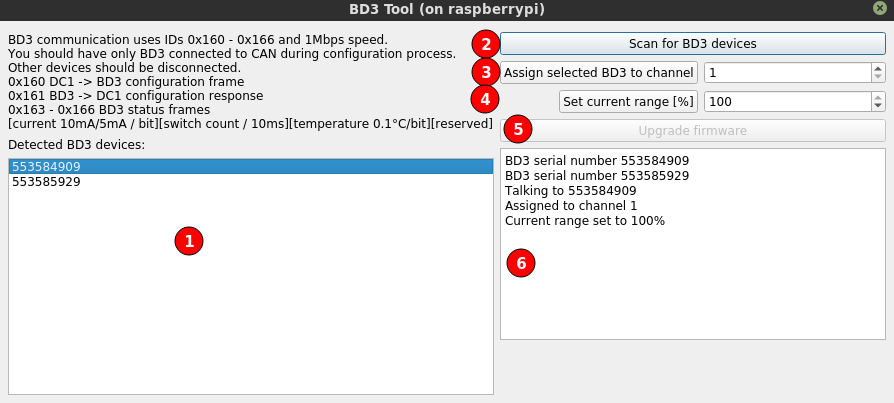
- Detected device list – click on the device serial number to configure it
- Scan again for BD3 devices – if the device was powered or connected after running BD3 tool
- Assign BD3 device to channel – the BD3 will know which current it should provide and on which ID it should send status message by using assigned channel information
- Set current range – sets device to provide fraction of BD3 nominal current (45A, 30A or 22.5A)
- Upgrade firmware – button is enabled if firmware in BD3 can be updated
- Log window – shows information what’s going on in communication between DC and BD3.
Channels
Up to 8 BD3 interfaces can be connected to DC dynamometer controller. Each one of the BD3 interfaces must be assigned to a distinct channel. Each Torque Controller in DC sends desired brake power fraction (0.0 ÷ 1.0) through CAN bus if “Send BD3 control message” is checked.
Example data flow:
Torque Controller 1 in DC ⇒ CAN bus message 0x162, channel 1 ⇒ BD3 programmed to channel 1 ⇒ CAN bus status frame 0x163 ⇒ DC
Torque Controller 2 in DC ⇒ CAN bus message 0x162, channel 2 ⇒ BD3 programmed to channel 2 ⇒ CAN bus status frame 0x164 ⇒ DC
Current range
The connected eddy current brake nominal current must be programmed into the BD3 interface. With use of this information, BD3 interface adjusts effective output voltage to keep your brake safe. Over-driving your absorber coils with current higher than nominal for some time can lead to coils damage!

Retarder electrical characteristic is connected with following equation:
- rated voltage = coils circuit resistance * current rating
If one of the parameters is missing in the specification, it can be calculated from the other two.
Example current range calculation for F16-120 absorber and BD3-22.5A:
Current range [%] = absorber current rating [A] / BD3 current rating [A] = 15.5A / 22.5A = 0.68 = 68%
Absorber nominal voltage rating
Supply voltage on L-L terminals | Desired absorber nominal voltage |
---|---|
230VAC or 400VAC | 192V |
120VAC | 96V |
Lower than desired absorber nominal voltages are supported, however:
- Current fluctuation around desired current target will be higher (average current will still be at desired value)
- As a result of higher current fluctuation, there will be higher absorber torque output pulsation and electrical noise emission
If you have absorber with lower than desired nominal voltage it would be the best to rewire it for higher voltage. Absorbers are usually made with 16 coils rated to 12V. Rewiring the absorber for higher voltage will require to connect all these coils in series (16*12V = 192V).
If absorber rewiring is not possible and current control is not satisfactory, BD3 power supply voltage can be lowered with use of transformer.
Minimum load resistances required for mains power supply option and BD3 version combination are listed below. Connecting lower resistance loads or shorting brake output will lead to device damage.
Supply voltage on L-L terminals | BD3-22.5A minimum load resistance | BD3-45A minimum load resistance |
---|---|---|
400VAC | 6.8 Ohm | 4.5 Ohm |
230VAC | 3.9 Ohm | 2.6 Ohm |
120VAC | 2.0 Ohm | 1.4 Ohm |
Avoiding EMI problems
The BD3 functions similarly to VFDs (Variable Frequency Drives) for electric motors. It uses high speed IGBT with high switching frequency to keep eddy current absorber winding current at desired level. During the IGBT turn on and turn off, fast voltage change occurs, which is called high dV/dt rate. This high switching frequency can lead to EMI (Electro-magnetic Interference) problems in the dyno test cell. These issues can manifest, i.e. as the dyno TV screen malfunctioning.
There are four paths of EMI transfer from the interference source to the interference victim:
- Conductive – through shared electric connection like power supply or signal cable
- Capacitive – through capacitance – large metallic area of source next to large metallic area of victim – this can be just cables laying next to each other – this path conducts interference from high dV/dt voltage change rates present at the brake cable and coils
- Inductive – through common inductance of source and victim – this can also be just source and victim cables laying next to each other
- Radiative – radiated and received through air by source and victim elements acting like antennas.
How to avoid EMI interference? Here are some low-cost guidelines you must adhere to, when designing the dyno components layout.
- Ensure that all metallic dyno elements are properly grounded – connected to building safety ground. The connections must be made with thick cables and have good conduction to the grounded elements. Here is a basic grounding checklist:
- Dyno frame
- Eddy current brake frame
- BD3 radiator
- DC controller safety ground pin in power connector
- Interference victim – monitor ground pin in power connector
- Cable shields
- Separate interference source cables from victim cables – power cables from signal cables. No signal cable should run near the BD3 – brake cable. You should also avoid running signal cables near power supply cables to the BD3 and high voltage capacitor cables.
- The high voltage capacitor must have as short connection as possible to the BD3. Short distance from BD3 to the brake will also reduce the possibility of interference.
- Use twisted pair cables, where required, i.e. CAN bus cable.
How to deal with EMI interference that is still present? If previous guidelines were not enough or were hard to implement, there are still some ways to save the day:
- Use cable shielding. The cable shield must be well grounded. In case of power cables, the shield can be grounded on both cable ends. The cable shielding helps to block dV/dt interference from travelling through capacitance between cables. You can shield interference source cables like BD3 – brake cable and capacitor cable. You can shield victim cables that receive the interference. You can shield both.
- Install common mode choke on BD3 – brake cable. These will block high frequency common-mode current path.
- Install ferrite rings / chokes on BD3 power supply cable.
- Install ferrite rings / chokes on victim cables. For example: HDMI cable.
- Install line filter on BD3 power supply cable. It will block conducted interference going to other devices through the building power supply.
- Install BD3 in a closed metal cabinet.
BD3 – absorber ferrite core cable choke
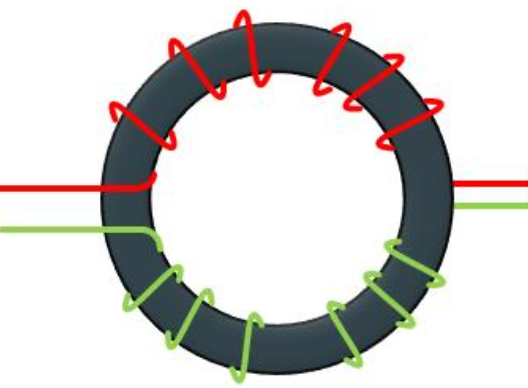
If BD3 to eddy current absorber cable is longer than 1.5m it’s advised to install a common mode choke on the cable. The choke can be easily made from a ferrite ring and some wire. Effective choke should have at least 0.5mH inductance. The equation for ferrite ring choke inductance is:
L = T² * AL
L – inductance
T – turns (winding) count
AL – ferrite core coefficient
Let’s go through example calculation. We can take a ferrite ring with dimensions 48mm x 30mm x 15mm with AL = 3200nH. Required inductance = 0.5mH = 500000nH
The required winding count T = sqrt(L/AL) = sqrt(500000nH / 3200nH) = 12.5
We divide the winding count by 2 and round up to give us 7 windings on each wire. Both wires must have same winding count. Take care to wind the wire in the correct direction. The wires from the BD3 should both come out from one side of the ring and the wires to the eddy brake, from the other side.
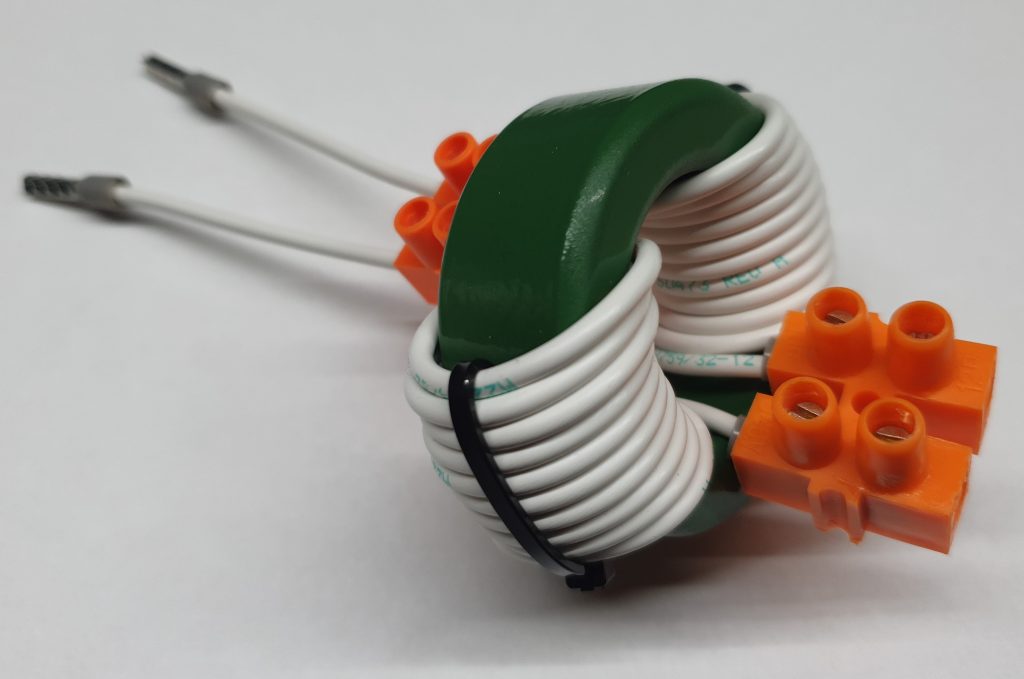
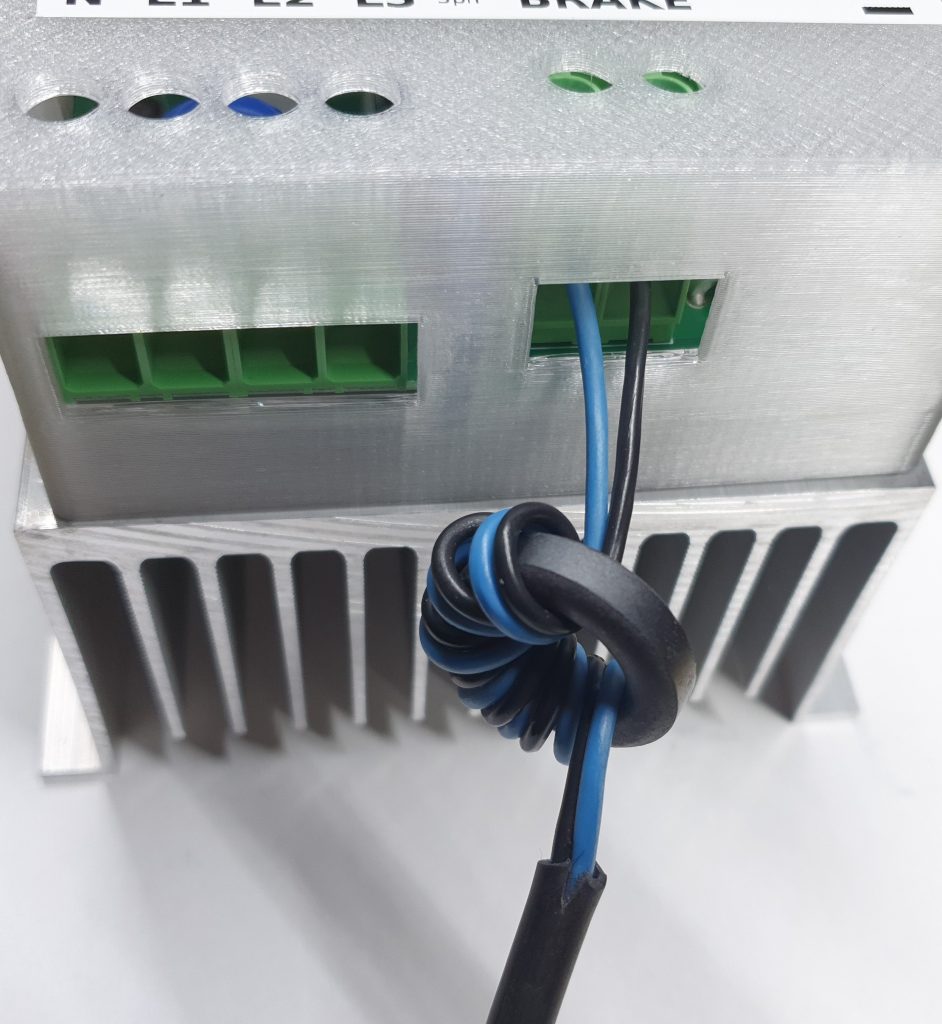
RCD protection nuisance tripping
If RCD protection trips upon powering up of BD3, then it is probably too sensitive for usage with this type of device, and it should be replaced by an RCD that is not that sensitive to disturbance. That can be an RCD with an additional delay, or higher trip current, or both.
Warranty
The producer guarantees that the device is manufactured according to accepted craftsmanship practices, and it meets the applicable standards. Correct device operation is guaranteed for 24-month period starting from date of purchase.
The guarantee does not cover damages caused by improper installation, usage or noncompliance with instruction manual.
The device is intended for installation by qualified personnel. Device final performance and suitability for a particular application is dependent on the user, and thus it is not guaranteed by the manufacturer.
These specifications are subject to change without notice.